3D Scanning, Reverse Engineering & 3D Printing a Motorcycle Seat
The Problem:
An updated approach to fabricating custom motorcycle components was desired by a manufacturer. In this instance, an aftermarket seat was to be designed and constructed.
Traditional Method:
The traditional method to producing a custom component like this seat would be to add and remove geometry from the customer’s supplied part with filler material, creating a master pattern, yet destroying the original seat.
This pattern is then used to create a fiberglass mold from which the manufacturer may fabricate their parts.
This method creates a few problems: the custom work and surface preparation of the pattern is a lengthy process, the customer cannot keep their stock seat for resale value purposes, and the manufacturer has no record of their master patterns in the event of a catastrophic loss, nor can they quickly build a catalogue without investing in every OEM part imaginable to destroy for the process described above.
NeoMetrix Solution:
The motorcycle seat was accurately digitized with Creaform’s HandySCAN hand-held 3D scanner in a matter of minutes. The manufacturer identified the critical mounting locations, and planned how the rest of the seat was to look.
Using Geomagic’s Design X reverse engineering software, the scan was converted to a finished 3D CAD model for production in a matter of hours, including all changes desired by the manufacturer.
The seat was then 3D printed in an appropriate material to withstand the temperatures required of the fiberglass molding process.
NeoMetrix Advantage:
First and foremost, the method proposed by NeoMetrix is non-destructive to customer parts. If the client decides they would like to keep their original bike components for resale value, they are free to do so.
With a handheld 3D scanner by Creaform, capturing data is fast and easy. Companies have a much easier time gaining access to OEM components if they do not have to alter or destroy them in the process. This will allow the manufacturer to build a significant catalogue BEFORE receiving orders, or in the very least have access to the data immediately upon receiving one, thus reducing time to market.
Having the ready-to-mold seat geometry pulled directly from the printer in a matter of hours is huge for time-to-market savings. Depending on the 3D printer selected for the job, some surface preparation may still be required for molding purposes, however this is only a small portion of the master pattern creation process.
Finally, the manufacturer will have digital backups of their entire catalogue. In the event a company their entire pattern/mold collection in a fire, hurricane, or other disaster, they must no longer start from scratch to rebuild their capabilities.
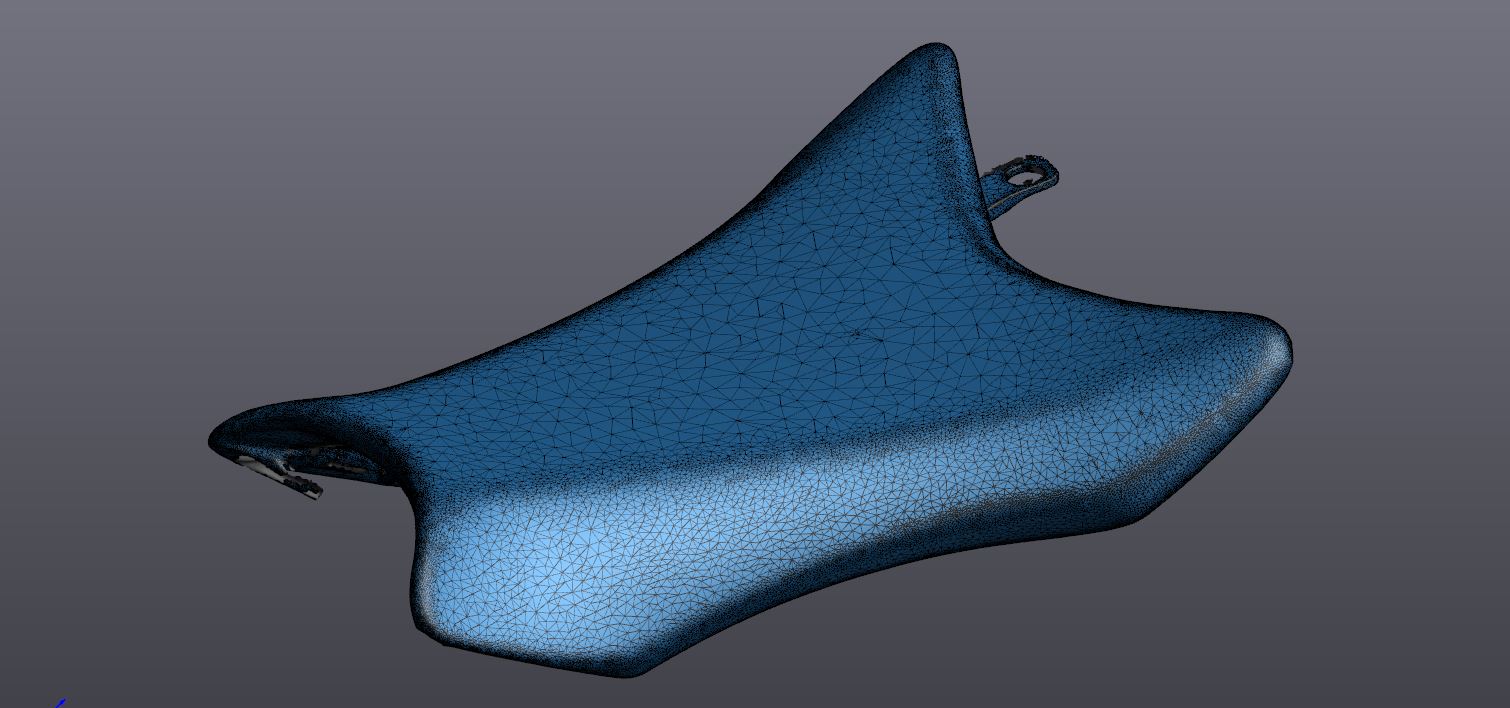
3D Scan Data – Top of Seat
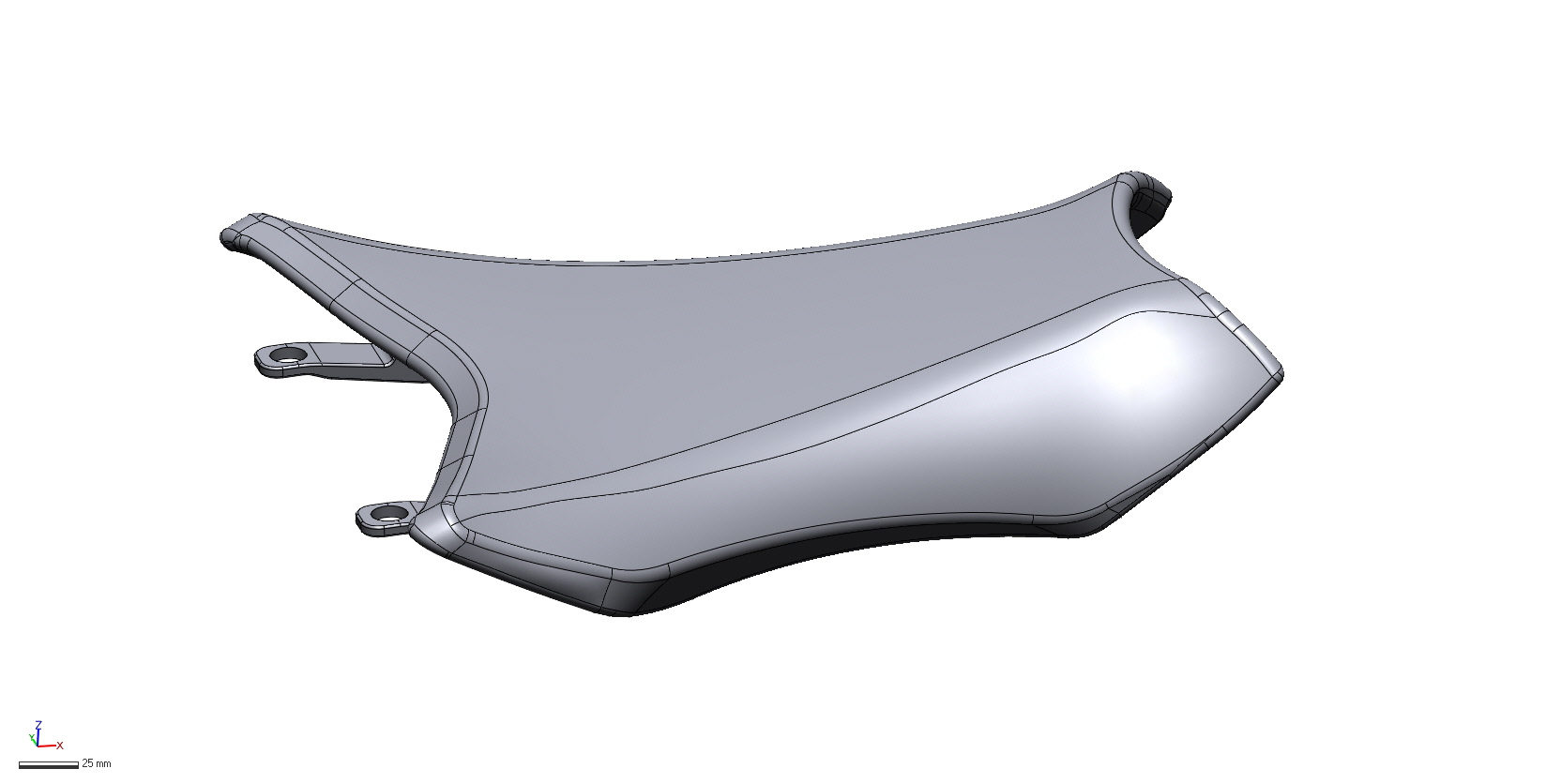
3D CAD Model – Top of Seat
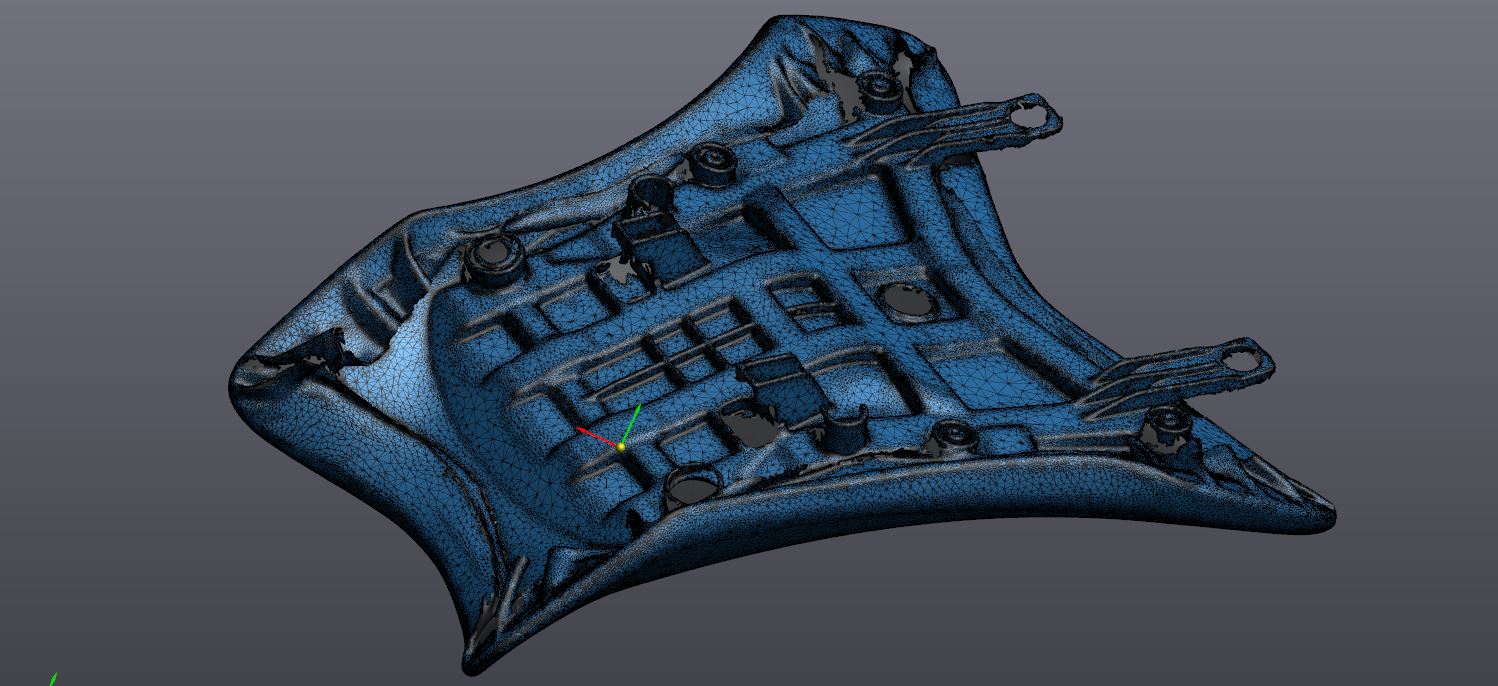
3D Scan Data – Bottom of Seat
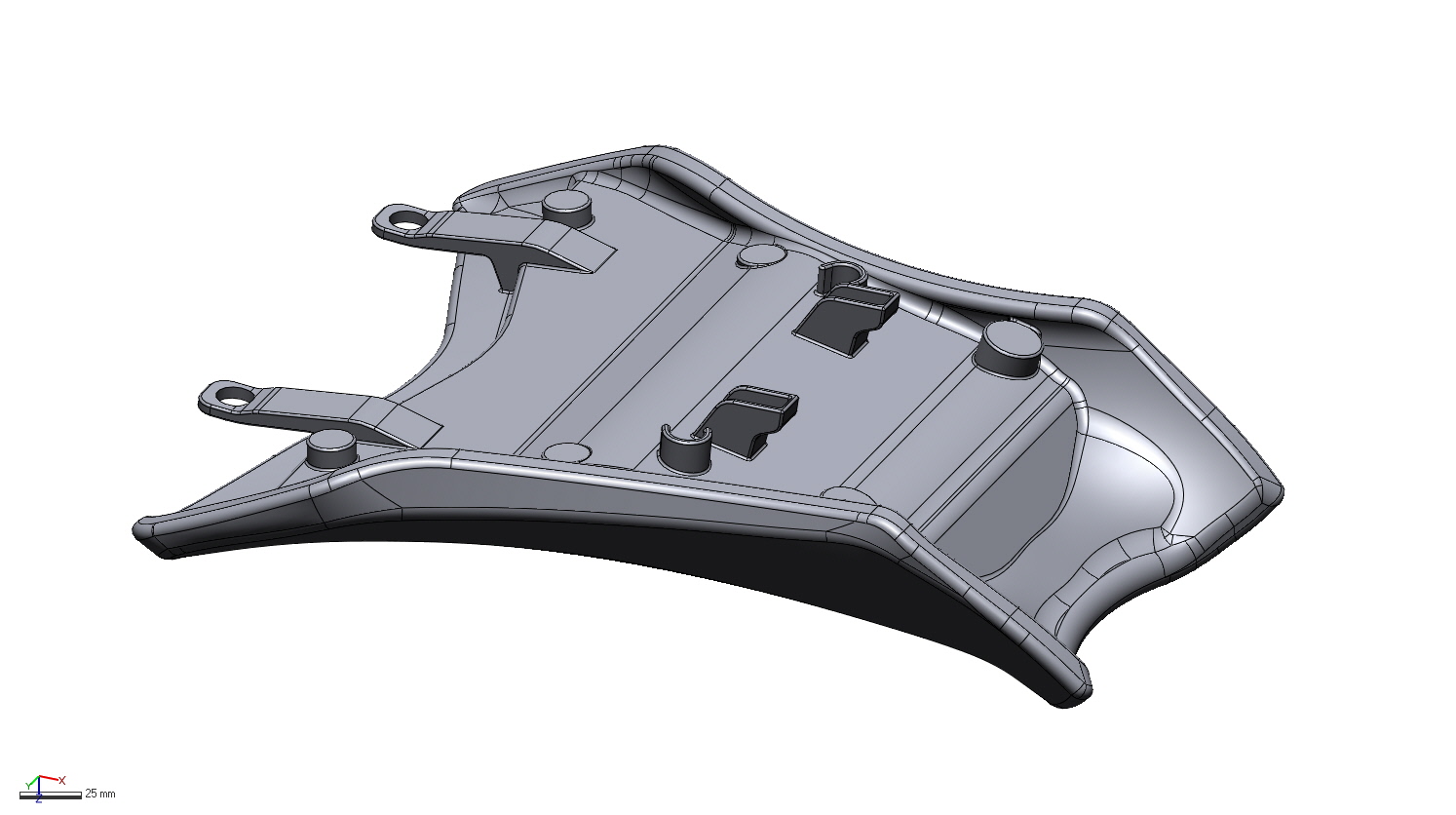
3D CAD Model – Bottom of Seat
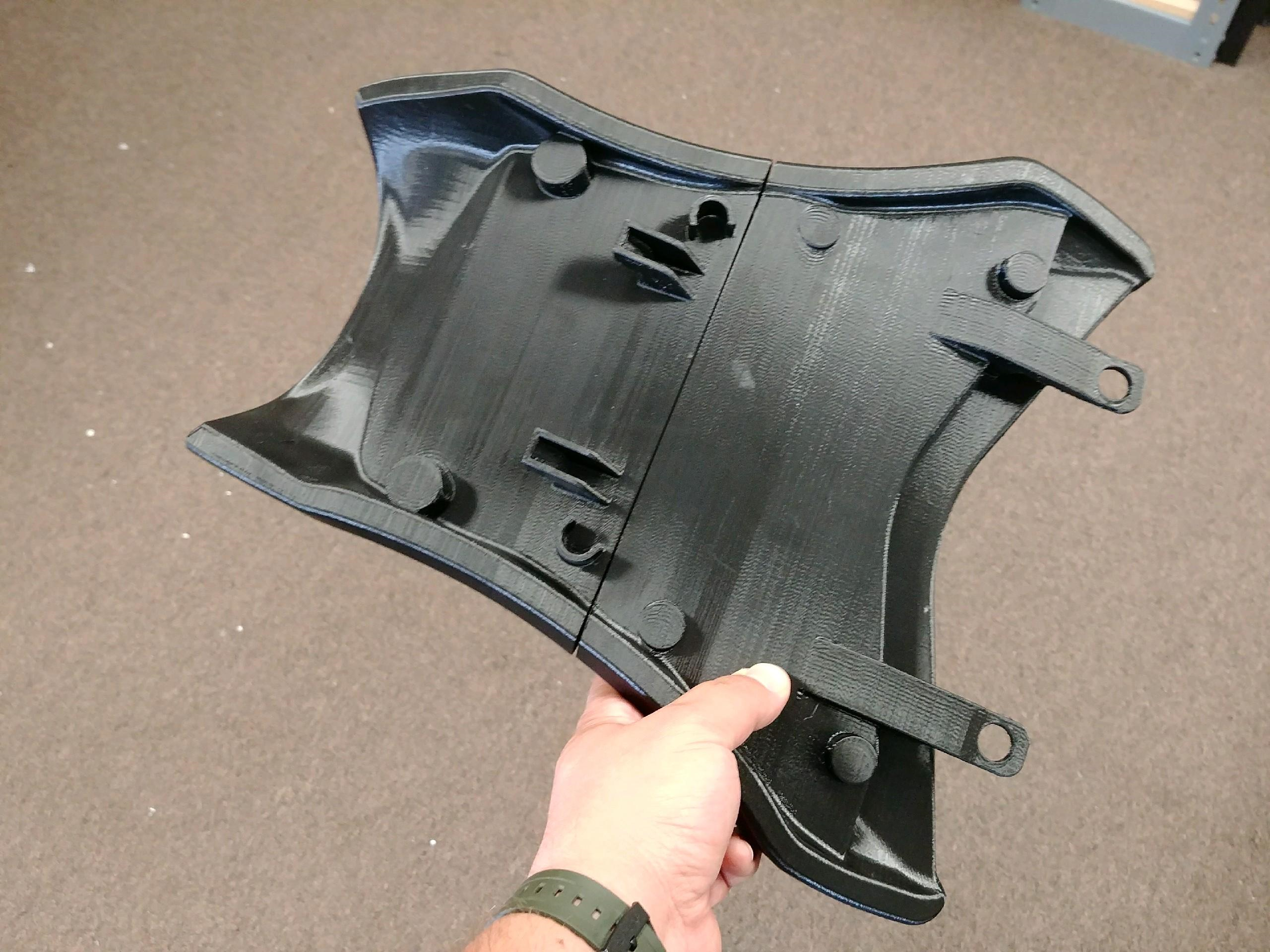
3D Printed Prototype of Motorcycle Seat