Problem:
Sporting Goods needs to reproduce a series of parts in order to put a new firearm into production. This requires a set of 3D models and 2D Drawings.
Traditional Method:
Hand measurements are normally used to pull off dimensions and radiuses. However, the complex shapes and angles were not features that could be accurately measured by hand.
NeoMetrix Solution:
3D Laser Scanning:
Using Konica Minolta’s Range 7 with a tolerance at .0015” the 3D mesh was brought into software to begin modeling. Requiring a fully parametric model, the Rapidform XOR software was chosen for its ability to not only create a parametric feature tree but to export out a solidworks file.
- Laser scan with Konica-Minolta Range 7 3D scanner accurate to .0015”
- Rapidform to align and merge multiple scans (Figure 2)
- Curves and sketches developed based upon scanned data to facilitate solid modeling.
- Accuracy analyzer used to verify accuracy of final model to original part.
NeoMetrix Advantage:
- Complex geometry accurately captured.
- Quick turnaround time.
- 100% Editable Solidworks part file to make future design changes.
- Ability to make a rapid prototype to check fit parts to existing mates.
Solidworks Live Transfer:
The machinist for Sporting Goods was familiar with Soildworks to create drawing and requested the final model be a Solidworks part file. Using Rapidform’s Livetransfer feature we can bring every feature in the parametric tree into the requested file type, giving him the ability to edit and change 100% of the delivered model.
Get Started Today!
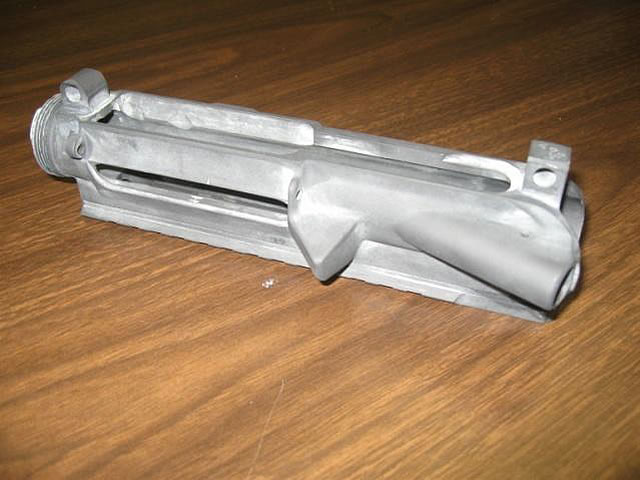
Figure 1 – Original Part
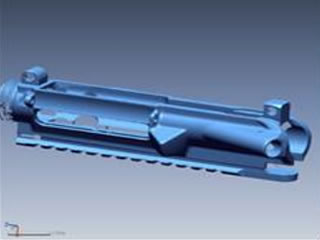
Figure 2 – Laser Scanned Data
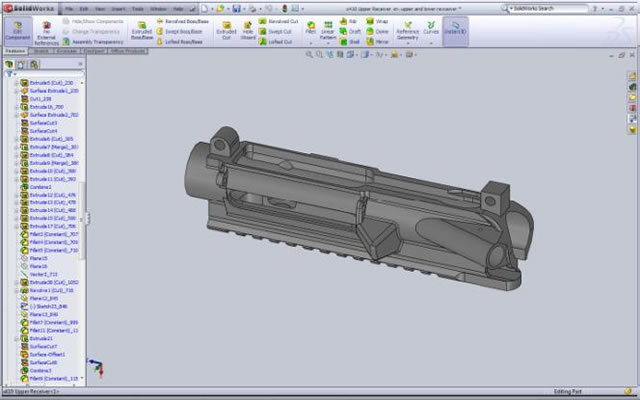
Figure 3 – Final Solidworks Model