3D Scanning & Printing Improves Shotgun Magazine Development
Black Aces Tactical Uses 3D Services from NeoMetrixTHE PROBLEM
The pump action shotgun, while a choice home defense and entry weapon, holds very limited ammo in its tubular magazine, and when empty is clumsy and slow to reload. Black Aces Tactical™ set out to bring the versatility of the Saiga-12 shotgun’s detachable box magazines to common pump-action shotgun models.
The first challenge to perform this alteration was gaining access to the geometry of the factory shotgun, as this is not made readily available by the manufacturer. The second was incorporating the necessary geometric changes to reliably accept a Saiga-12 magazine.
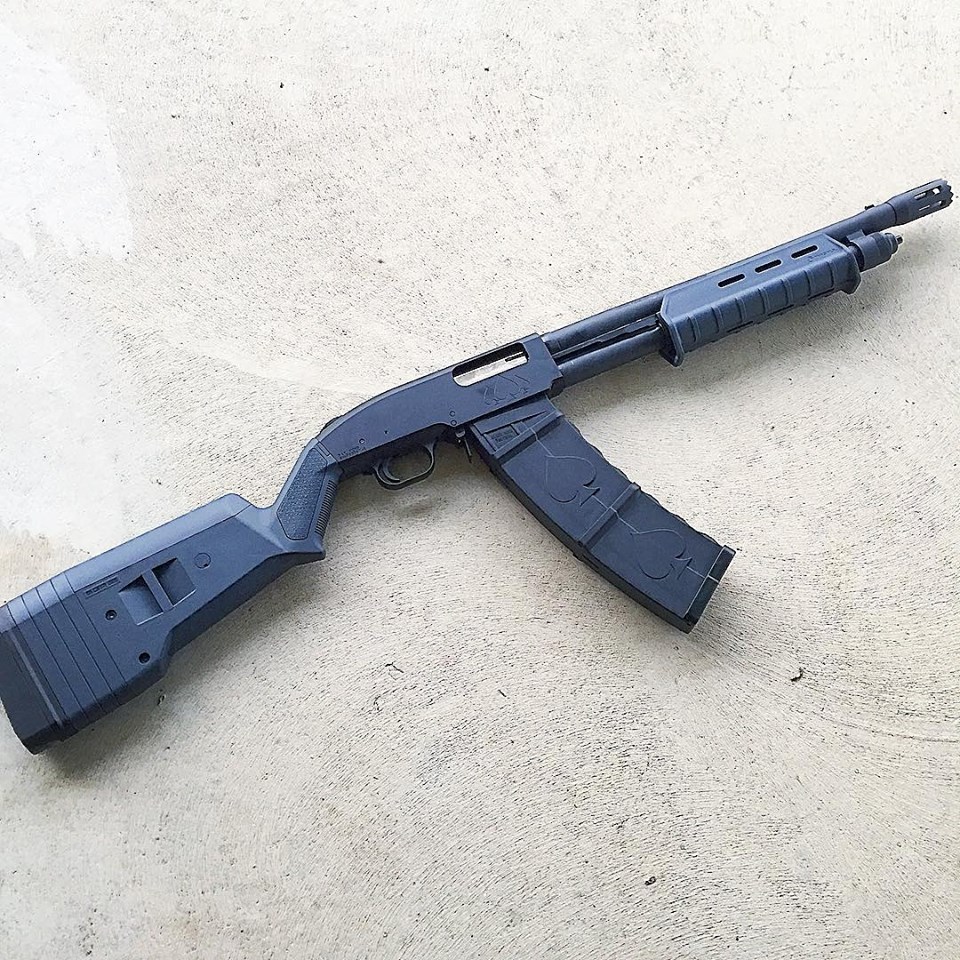
TRADITIONAL METHOD
The standard reverse engineering method would be to take measurements of both shotgun receivers and essential components by hand. This in itself lends the potential to incorporate human error. Combine this with the difficulty of marrying the geometries from two unrelated firearms, while retaining unfailing reliability, and one can begin to see the magnitude of this undertaking.
NEOMETRIX SOLUTION
A Mossberg™ 500 receiver and components, as well as a Saiga-12 shotgun receiver, were 3D scanned using a Zeiss Comet L3D structured light 3D scanner for optimum resolution and accuracy. Individual shots were quickly merged into triangulated meshes using Zeiss’ CometPLUS acquisition software.
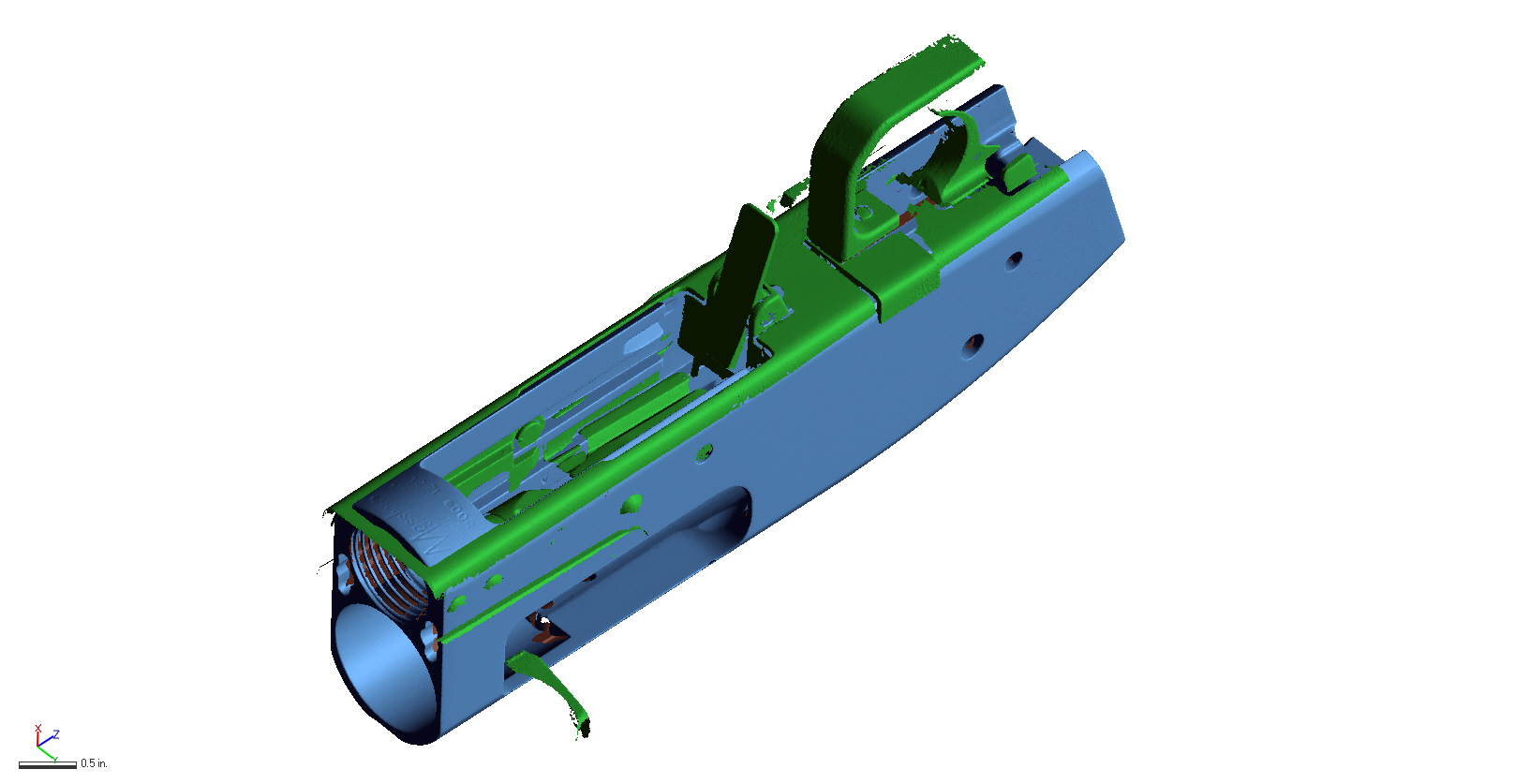
These meshes were imported and aligned using key geometry in Geomagic Design X software for reverse engineering, and a 3D CAD model of a new receiver was created. This new receiver utilized the Mossberg™ design as the basis, and incorporated the proper geometry to accept the Saiga-12 magazine.
From this CAD file, a working prototype receiver was machined and assembled. Through testing, receiver geometry was fine tuned by hand to ensure absolute reliability.
Once the prototype receiver functioned flawlessly, NeoMetrix Technologies scanned it as well. This new scan was overlaid on the original CAD file, and the hand-worked geometry was incorporated into the final model using Geomagic and ANSYS SpaceClaim Engineer. It was from this revised CAD model that production receivers were made.
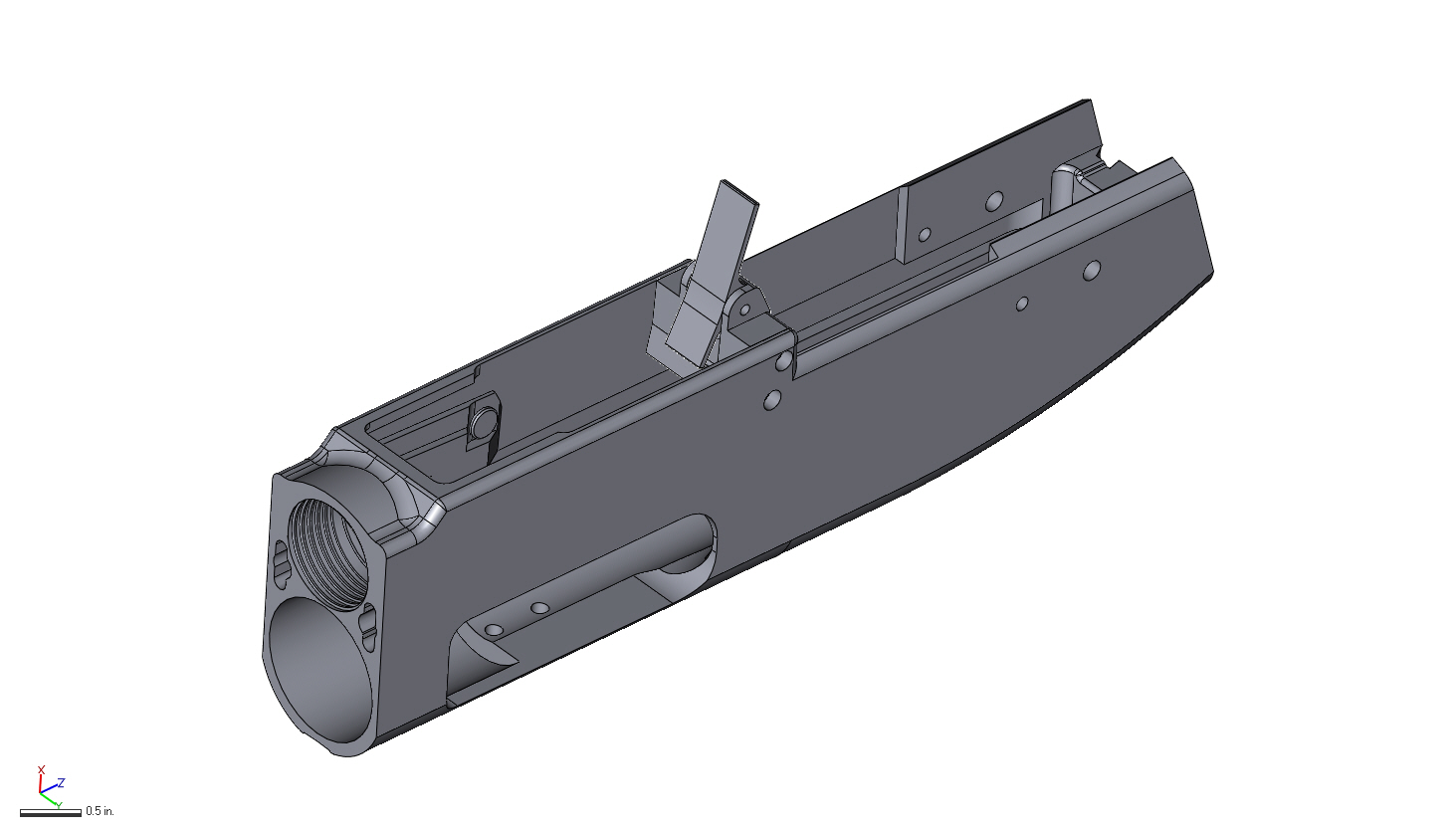
NEOMETRIX ADVANTAGE
In the data acquisition stage, 3D scanning quickly provides a complete data set with accurate locations and dimensions of all parts within the assembly. This is an immediate advantage over taking hand measurements of the individual components, and then attempting to accurately measure where they are located within the assembly.
3D scanning is not subject to the same error-stacking that may occur by hand-measuring from feature to feature.
When modeling the combined receiver, the 3D scanned data sets provided an excellent visual aid of how the two must be overlaid, and where the essential geometries of both assemblies must be modeled in space.
Once the prototype was hand-tweaked and critical geometries altered, the manufacturer had no accurate method of quantifying these changes for final production. A 3D scan of the final prototype overlaid on the initial CAD file allowed quick identification of where and by how much the originally geometry had been modified. The model was updated to reflect these changes for production.
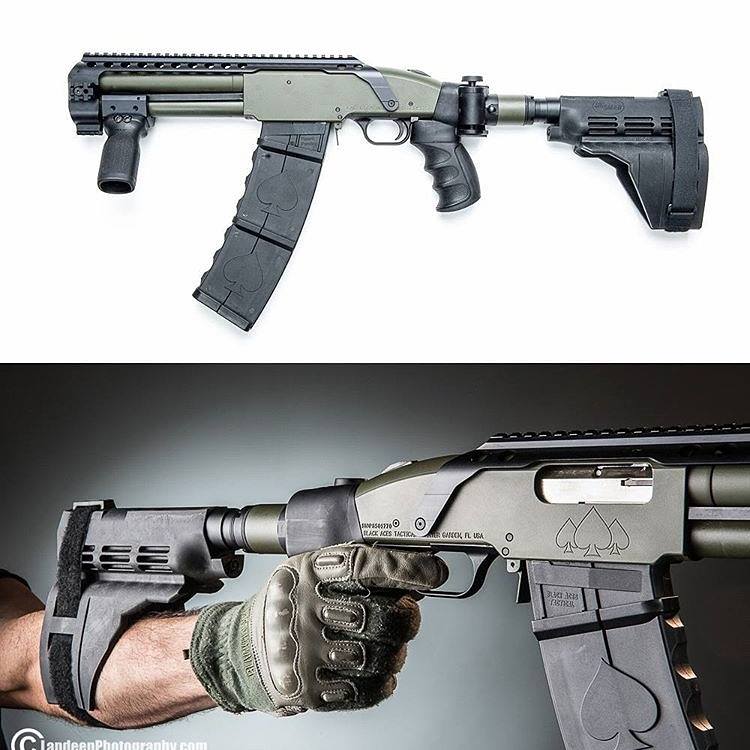
For more information on Black Aces Tactical’s Pro Series 5 shotguns, you may reach them via the following:
sales@blackacestactical.com
(407) 919-9783