Re-Engineering a Metal Detector
Spot Industries Redesigns Metal Detector ShovelThe Concept
Spot Industries came to NeoMetrix with a hand-made prototype for a portable shovel that incorporates a metal-detection device. The initial prototype (Fig. 1) consisted of a collage of off-the-shelf parts manipulated and assembled in a way to closely represent the vision for the end-product. Although this prototype was functional enough to analyze certain factors during the proof-of-concept stage such as form, fit and function, Spot Industries wished to develop some custom features as well as design a clean model for future production.
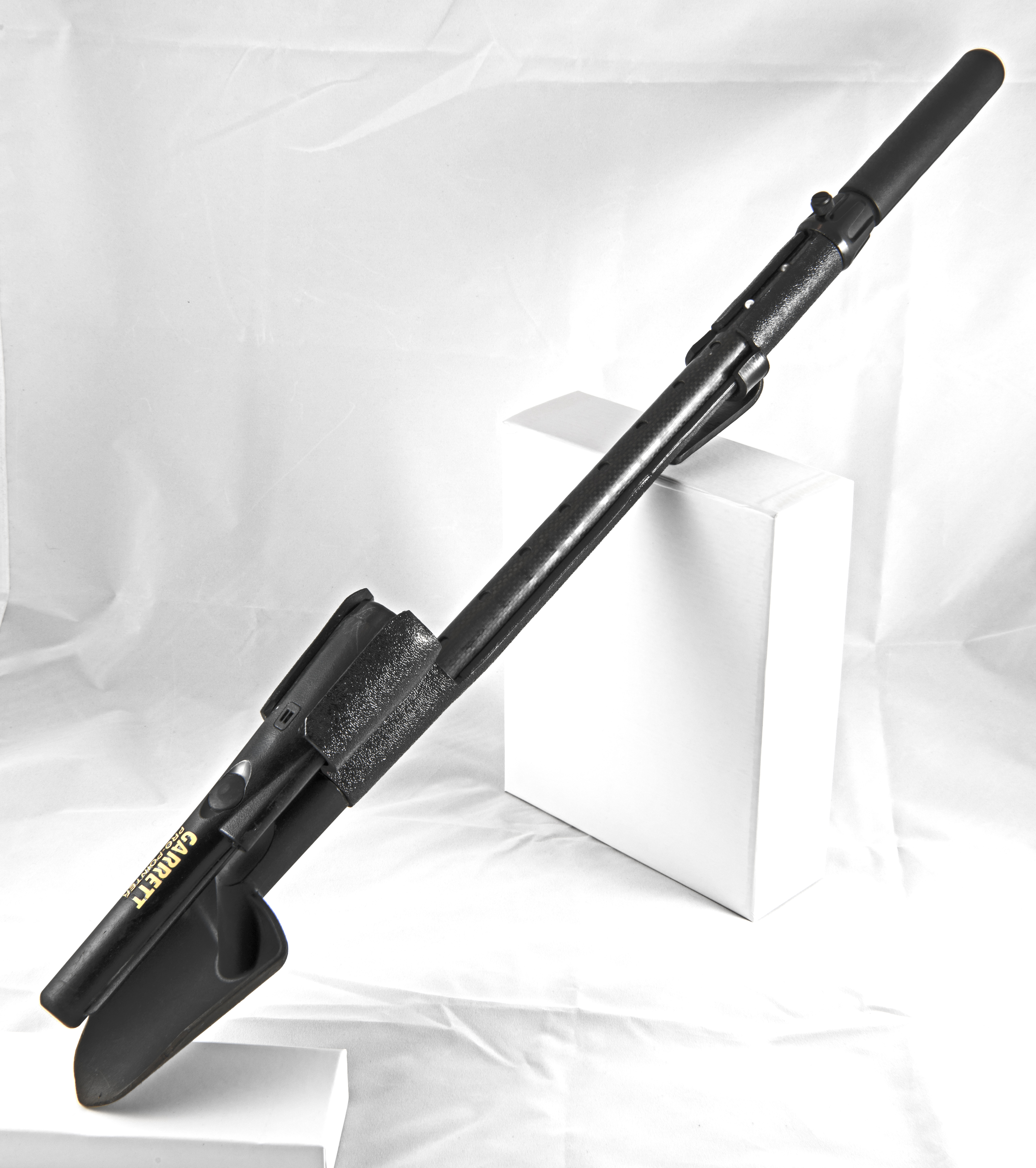
Fig1. – Hand-Made Prototype Shovel with Metal Detector
The 3D Scanning Advantage
Using the Zeiss L3D 5M 3D scanner, Neometrix was able to scan each individual part as well as the assembly, and then orient each scan to their corresponding location in the assembly (Fig. 2). These scans would serve as a baseline guide in order to create accurate CAD models of each component while simultaneously integrating the requested custom features and dimensions provided by Spot Industries (Fig. 3).
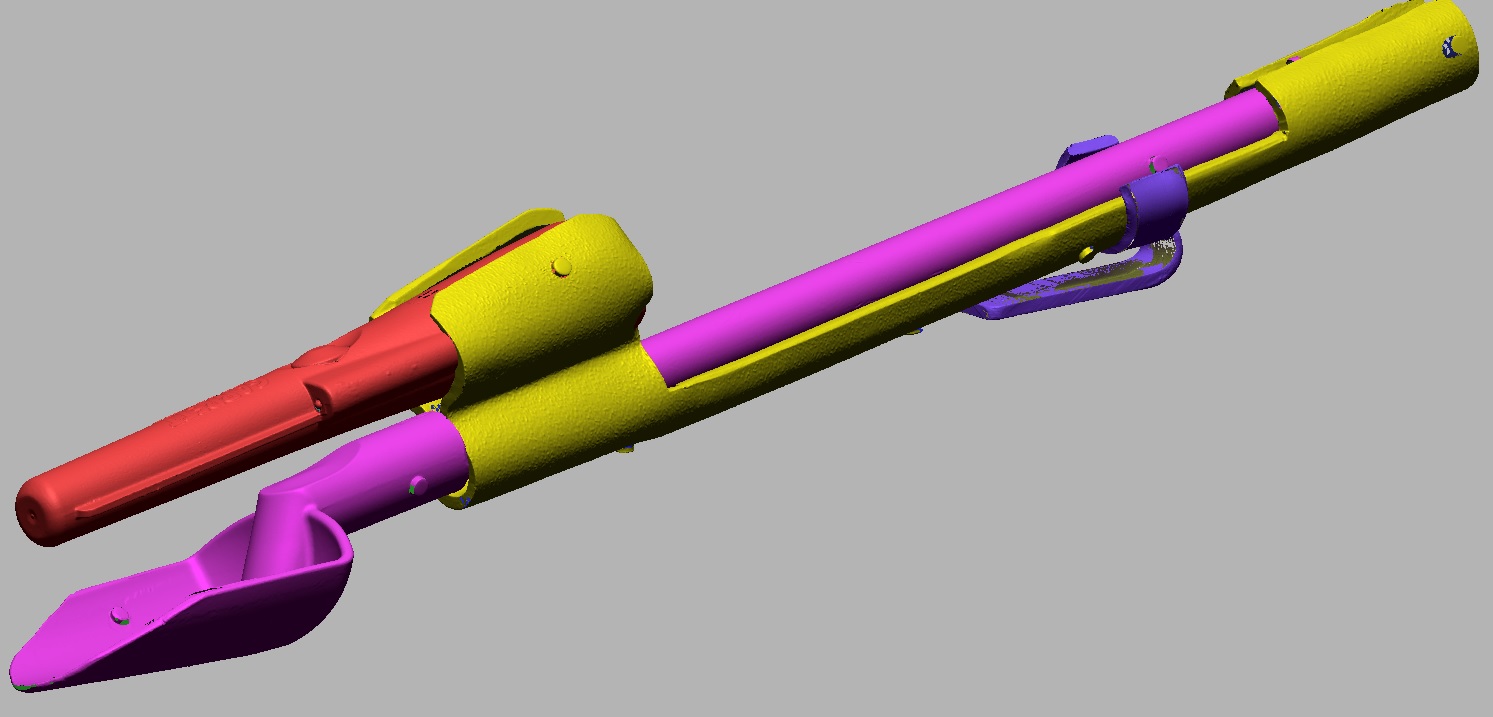
Fig2. – Scanned Data of Each Component
One-Stop Shop
Once the CAD model was finalized, the next stage in the process was to 3D print a prototype of the newer design using NeoMetrix’s Stratasys Connex 3D printer. The shovel head, main housing and belt clip were printed in Digital ABS material (Fig. 4) while the round tubing and grip would be sourced from bulk elsewhere. Finally, fit and clearance were confirmed by mounting existing parts to the printed parts.
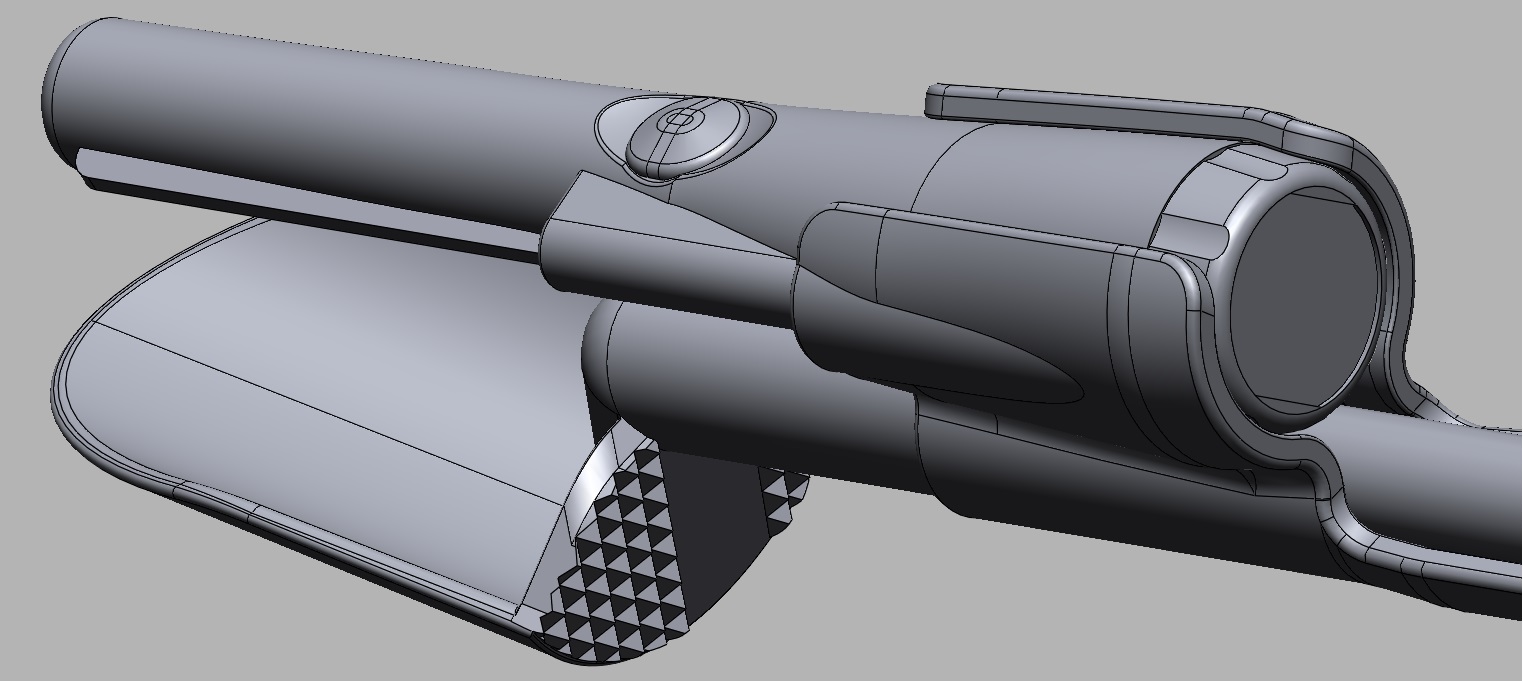
Fig 3. – Final CAD Model Generated from Scanned Data
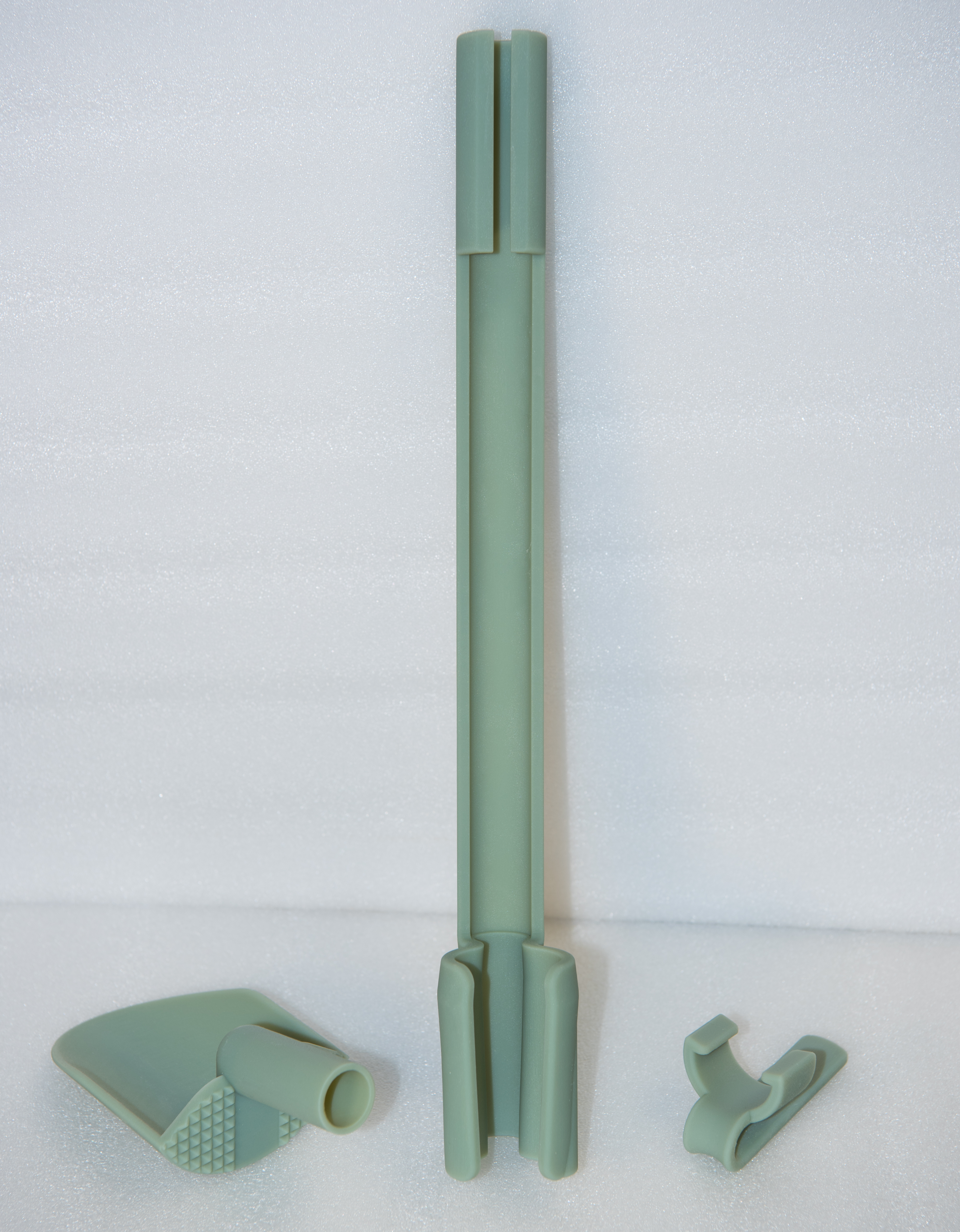
Fig 4. – 3D Printed Parts