3D Scanning of a Hard Hat
The Problem:
Students at the Florida Atlantic University were tasked with designing accessories for a standard hard hat as part of their senior design project. New components need to fit correctly to the existing geometry, as well as avoid any interference with existing accessories, such as hearing protection and the eye safety shield. As such, they required a 3D CAD model to use as a reference for their design.
Traditional Method:
The traditional method of reverse engineering, or 3D modeling and existing design employs the use of hand tools, such as tape measures and calipers. Complex contoured shapes sometimes require a little additional creativity in the development of cardboard templates trimmed to match the contours of the object at various locations. All this data is then compiled and manually entered into a CAD systems, such as SolidWorks.
The problems with these methods are immediately obvious:
- One dimensional measuring tools cannot capture complex geometry
- Hand cut templates are often inaccurate
- There is no way to check the final model back to the original data used to create it
NeoMetrix Solution:
The NeoMetrix solution to these issues is to employ the use of 3D scanning. In this case, the Creaform MetraSCAN was used to rapidly scan the existing geometry of the hard hat directly into the computer. VX Elements software is used to immediately process the scanned data into a fully optimized polygonal mesh saved at the desired resolution for this application.
That mesh is exported as an STL file, then imported into Geomagic Design X software for clean up, and processing into a “rapid surface” model. This final model can then be imported into the end user’s CAD system, in this case Solidworks, for uses as a reference when designing new components.
The final model can then be compared back to the original scan to ensure that the final result is accurate to the original.
NeoMetrix Advantage:
There are two primary advantages to using 3D scanning for reverse engineering and 3D modeling of existing parts: speed & accuracy.
The Creaform MetraSCAN is accurate to better than .001” on a part of this size, and modeling the hard hat from this type of data is significantly faster than taking a series of tedious measurements and manually entering them into CAD.
These two factors ensure that new parts designed to interact with the existing hardware can be developed quickly and have a perfect fit.
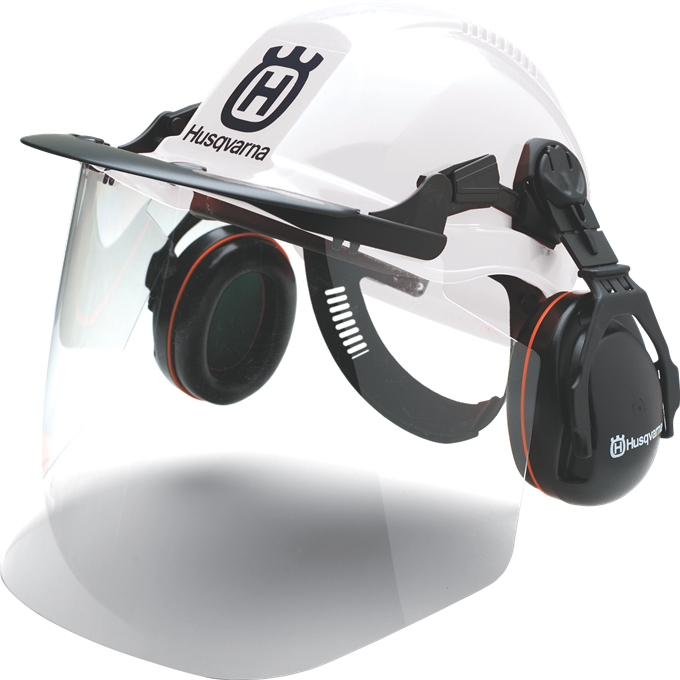
Hard Hat to be Scanned
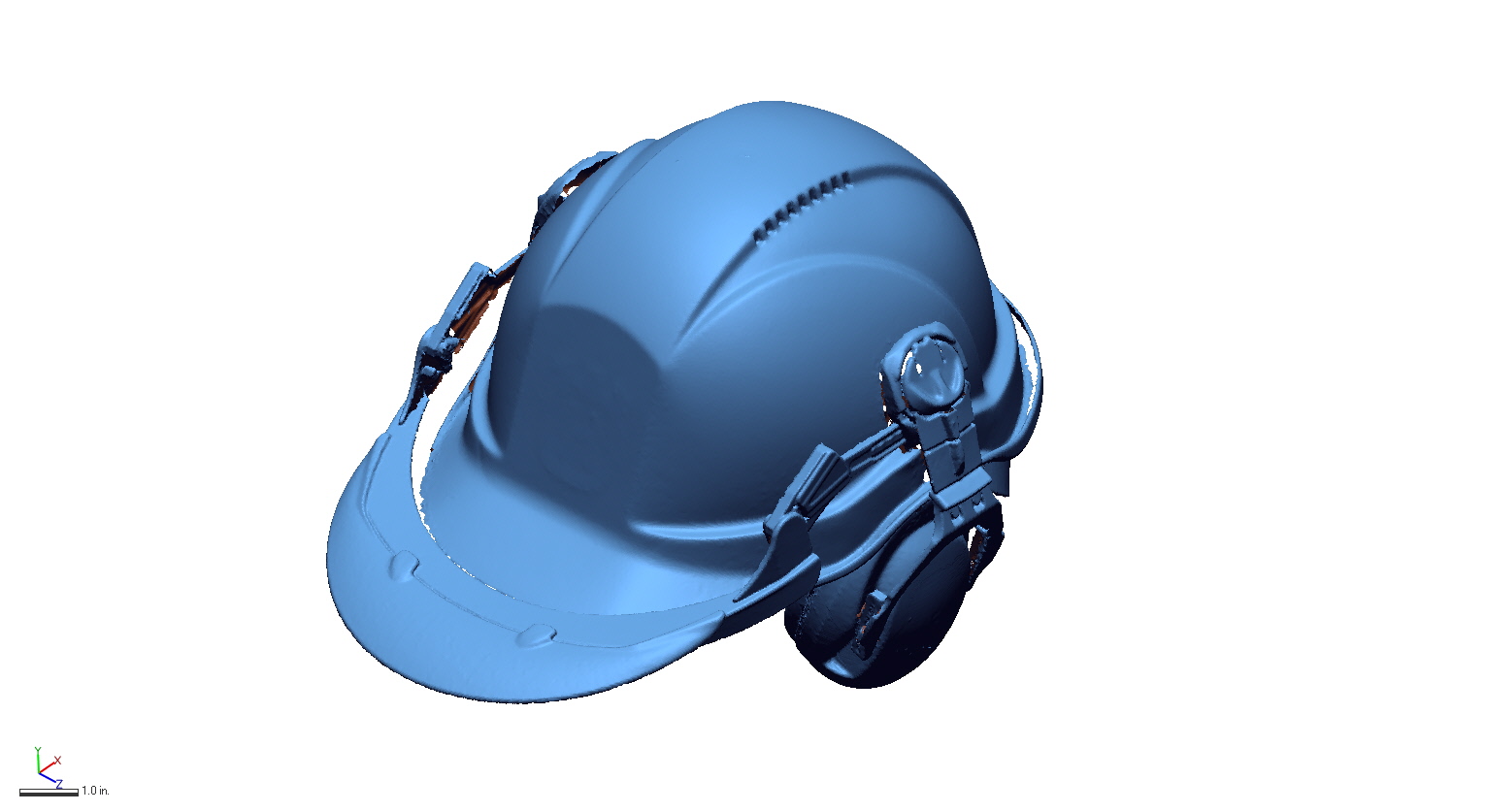
Hard Hat Scanned Data
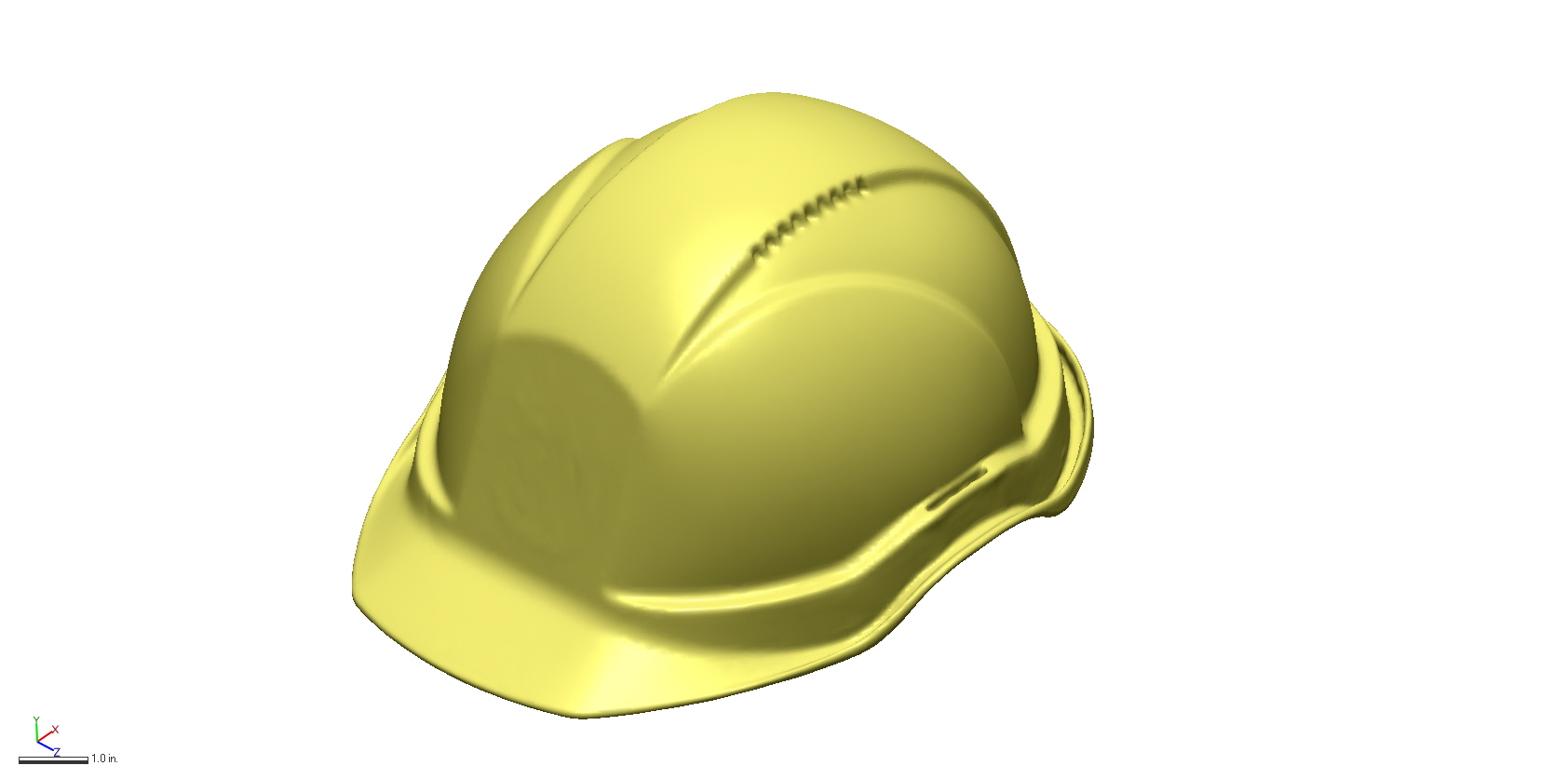
Hard Hat Surface Model
The students’ project, The Smart and Safe Tractus (S&S Tractus) is a next generation device aimed to significantly improve worker safety in the power industry. It allows its users to record hazard logs with automated speech recognition with timestamp and GPS coordinates, make phone calls, and take photos and stream video of their current tasks, all with the push of a button. It provides warnings to the user when high voltage objects are within an unsafe range and alerts the user of other documented safety issues. A companion IOS mobile application enhances the capabilities of the S&S Tractus with features such as user authentication, hazard documentation, access to substation diagrams and tutorial videos, and a phone call user interface.
With our cutting-edge 3D scanning technology, we were able to provide the students with great results. According to Anthony Goish, a member of the project team, “Our project was a success. Thank you (NeoMetrix Technologies) helps…everyone was impressed with the design and all the systems functioned as intended…What an amazing technology. Thank you for your help”
Below are images of the students’ project: